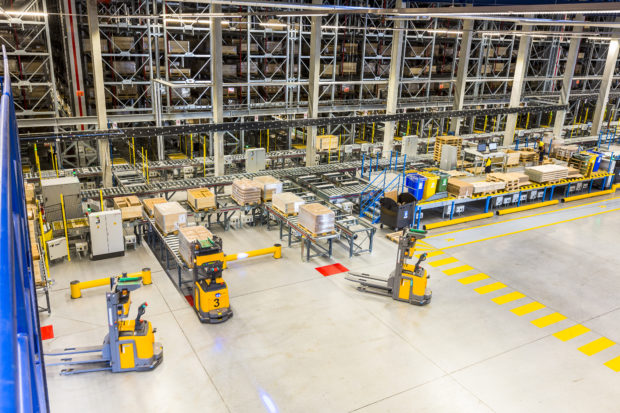
Závod IKEA Components v Malackách balí skrutky, drevené kolíky a ďalšie komponenty, potrebné pre montáž nábytku, a distribuuje ich ďalej výrobcom nábytku, ktorí sú dodávateľmi IKEA. Aby všetko bežalo, ako má, ani tomuto závodu sa nevyhla automatizácia.
O to, aby sa milióny súčiastok v závode IKEA Components dostali včas na svoje miesto sa dnes stará aj štrnásť úplne automatizovaných a bezobslužných vozíkov Jungheinrich. Podľa plánu dokáže po rozšírení kapacít v budúcom roku 21 týchto vozíkov denne prepraviť takmer štyri tisíc paliet.
Pri projekte treba niekedy začať od konca
Dodávatelia IKEA sa postupne prispôsobujú plánom tohto koncernu do roku 2020 zdvojnásobiť objem predaja. Slovenský závod IKEA Components na Záhorí, ktorý balí a predáva kovania jednotlivým výrobcom nábytku IKEA do známych vrecúšok a kartónových krabičiek sa musel prispôsobiť tiež. „My sme našu prevádzku už niekoľko krát rozširovali, ale v roku 2014 sme sa rozhodli, že ďalšie rozšírenie bude také zásadné, aby sme mali rezervy na niekoľko rokov dopredu,“ hovorí Ľuboš Lesay, vedúci projektu Stavba a technológia v rámci expanzie IKEA Components.
Firma si spočítala, že do roku 2020 bude potrebovať výrazne väčšiu fabriku, ako mala v roku 2014. Bolo treba vybudovať nový a moderný výškový sklad a pristavať dve nové baliarenské haly s technickým a administratívnym zázemím. Podarilo sa vďaka tomu rozdeliť priestory tak, aby materiál logicky prúdil z jedného konca závodu na druhý a počas tejto cesty ho vedeli spracovať. Keď sa takto nadefinoval cieľový stav a jednotlivé procesy výroby, bolo možné začať sa zaoberať tým, ako zabezpečiť dopravu tovaru v rámci závodu.
Išlo o veľkú výzvu, pretože po plnom rozbehnutí produkcie v roku 2020 bude musieť denne túto trasu absolvovať 2250 paliet s tovarom do výroby a podobné množstvo potom pozbierať a dostať do expedičného skladu. „Keď sme si predstavili, že by sme to mali zvládnuť s rovnakou technológiou ako doteraz a všetko voziť na klasických vozíkoch, bolo nám jasné, že to nie je tá správna cesta. Bolo by treba zamestnať veľa nových ľudí, museli by sme postaviť väčšie haly a navyše by sme sa nevyhli chybám a nehodám,“ hovorí Ľuboš Lesay.
Návratnosť tejto investície je šesť rokov
Preto vo firme začali hľadať riešenie, ktoré by zautomatizovalo tento pohyb tovaru aspoň na tej najdôležitejšej dopravnej tepne v závode. Požadovali flexibilitu systému, preto úplne vylúčili dopravníkové systémy a tak isto sa im nepáčili vozíky navádzané magnetickými páskami alebo rôznymi inými, dnes už prekonanými technológiami.
Firma tak začala hľadať dodávateľa, ktorý by vedel dodať vysokozdvižné vozíky navádzane laserom, ktoré sú schopné úplne bez obsluhy prepravovať palety podľa potreby na rôzne miesta v sklade a sú cenovo dostupné. Najlepšiu ponuku nielen na vozíky, ale aj celý tento systém predložila spoločnosť Jungheinrich. O víťazovi nerozhodla iba dobrá cena, ale aj celková flexibilita systému, ktorý vedeli prispôsobiť našim podmienkam v závode. A v neposlednom rade aj moderné riešenie automatických vozíkov.
„Do IKEA Components sme dodávali vysokozdvižné vozíky, ktoré majú lítium iónové batérie a teda sa môžu nabíjať podľa potreby, takže netreba čakať na ich úplné nabitie,“ hovorí Martin Urban, konateľ spoločnosti Jungheinrich. Vďaka tomu nie je nutné mať špeciálnu miestnosť na nabíjanie, firma ušetrí aj na náhradných batériách a s tým súvisiacej údržbe a predovšetkým sa získal čas.
Dôležitým faktorom bola aj blízkosť a kvalita servisu. „Keď sme si to spočítali, tak nám návratnosť komplexnej investície do rozšírenia skladového systému vyšla okolo šesť rokov,“ dodáva Ľuboš Lesay.
Veľká výhoda – vozíky jazdia sami
Dnes už v hale pracuje 14 automatických vozíkov, ktoré úplne bez obsluhy jazdia do skladu, odkiaľ vyzdvihujú palety a podľa potreby ich doručia na odberné miesta vo výrobe. A naopak, keď sú kovania zabalené tak, ako majú byť, vozík sám príde a odvezie paletu do expedičného skladu na cestu ku klientovi.
Keďže ide o laserom navádzané vozíky, tie vždy presne vedia, kde sú. Pomocou senzorov neustále monitorujú priestor okolo seba, takže riziko zrážky s ľuďmi alebo inou technikou je minimálne. Vďaka tomu môže byť tento systém v jednej hale spolu s bežnými vozíkmi, ktorých obsluhujú manipulátori alebo priamo s ľuďmi vo výrobe.
Chvíľku trvalo, kým si ľudia zvykli na to, že vozík naozaj vždy pred nimi zastaví, ak je treba, ale skúsenosti nás presvedčili, že systém je bezpečný, treba sa s ním však naučiť spolužiť. Zabudnutá paleta, položená pred miesto, kde má vozík odovzdať tovar totiž môže na niekoľko minút zastaviť prácu vozíkov a vytvorí sa menšia zápcha. Automatické vozíky ju síce vidia, ale keďže ju tam dal človek, tak ju nemôžu posunúť vedľa tak ako býva zvykom. No a na toto si ešte ľudia musia zvyknúť.
„Skúsenosti z prvých mesiacov ukazujú, že sme sa rozhodli dobre a automatizovaný systém nám pomáha byť efektívnejší a rýchlejší ako keby sme ostali pri klasickom riešení,“ hovorí Ľuboš Lesay.